€8m fan test facility in operation
GERMANY: Fan specialist EBM-Papst has brought its new €8m testing centre into operation after a 15-month construction period.
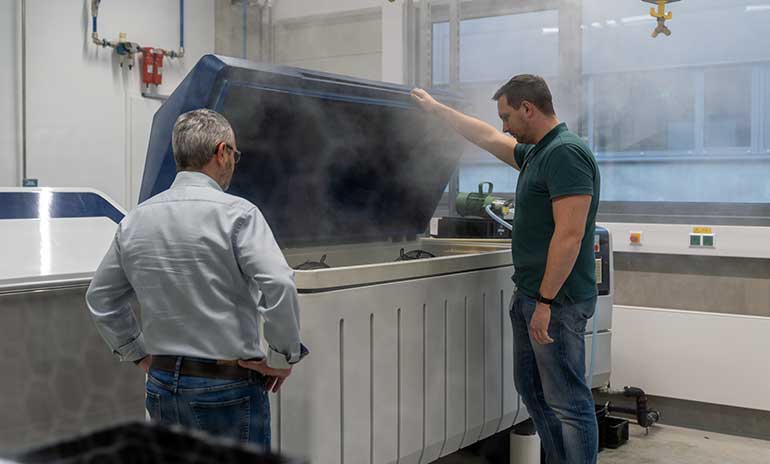
The new 2,500m² facility centralises all the company’s testing operations carried out at its Mulfingen headquarters.
EBM-Papst recognises that the service life, performance and long-term behaviour of fans are influenced by their environment throughout their entire service life. In six test bays, several hundred fans and individual components per year will be brought to and beyond their stress limits under real environmental influences.
Fans often travel long distances before they reach their final place of use and storage and transportation can have an impact on service life even before commissioning. For this reason, stresses that can occur during transportation are simulated using sustained vibrations of varying intensity and individual shock pulses.
In climatic chambers, the fans are subjected to rapid temperature changes in order to rule out possible weak points, material fractures or material connections in advance. They also prove that they can withstand moisture in five standard tests based on IP X3 to IP X6 and IP X9K.
Individual components are also put under the microscope. In the spin test, both during development and when new sizes of existing series are introduced, the impellers are brought up to and above their maximum operating speed in order to determine the destruction speed.
A salt spray corrosion test wets specimens with a salt spray in closed chambers to ensure the quality of the coatings and welding points.
In order to work reliably in practice over many tens of thousands of operating hours or longer, fans must also be able to cope with a combination of stress types. Specifically for this purpose, EBM-Papst has developed three accelerated service life tests that simulate an entire product life in fast motion over several months.
Back to top button